Get a quote, configure a custom safety solution or ask a question. We're here to help!




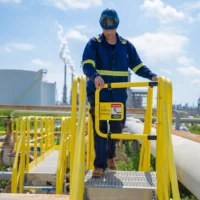



- Spill ContainmentMore …Loading Safety CagesMore …
SafeRack Worldwide
We pride ourselves on one-on-one customer service. When you call SafeRack, we'll be there to answer your questions with a combined experience of 400+ years.
Select your region below.- View Products
- Railcar & Truck Loading Platforms
- Gangways & Loading Ramps
- Stairs, Platforms & Ladders
- Mobile Ladders & Platforms
- Loading Arms & Fluid Transfer
- Safety Gates & Traffic Control
- Aviation & Aerospace Access
- Marine Access & Loading
- Grounding & Monitoring
- Spill Containment
- Loading Safety Cages
- Transloaders & Skids
- Shelters & Canopies
- Fall Protection
- Terminal & Speciality
Home / Industries / Bulk Chemical Loading / ChlorineChlorine Handling Design, Loading, and Installation.
Although no two Chlorine Loading solutions will be identical, the product itself determines much of the critical design criteria that will ensure that optimum safety and productivity can work together in harmony.
What is Chlorine? Chlorine is a naturally-occurring chemical element, one of the basic building blocks of matter. Scattered throughout the rocks of Earth’s continents and concentrated in its salty oceans, chlorine is an essential nutrient for plants and animals.
In the United States, chlorine is a “tight-fill” (closed-loop) loading operation and is loaded into trucks or railcars via chemical hoses or by-pass arms. Chlorine, if not handled properly can be fatal and Personal Protective Equipment (PPE) is required. Additionally, because operators are on top of the vehicles during the loading process, fall prevention is essential, not only for safety but increases throughput.Chlorine tank cars are top un-loaded by increasing the pressure in the vapor space above the liquid level to force the chlorine up the discharge pipe and out the liquid angle valves. Connections to the Angle valves are typically made from one-inch schedule 80 carbon steel pipe, approximately 15” long with standard NPT threaded ends. Additional padding (increasing the pressure in the vapor space) with compressed dry air or nitrogen can be used if the tank car pressure drops during the unloading process.
Question, Get a Quote, Live Demo or Request an On-Site Visit
Our experts simplify the complex
View Full TextChlorine is transported DOT 105 class dedicated thermal insulated and pressurized railcars and DOT MC-330 & MC-331 Truck tank trailers
18,000 to 23,000-gallon DOT 105 class dedicated thermal insulated and pressurized tank railcars are used to transport Chlorine on rail. Chlorine tank railcars come in three sizes 55, 85 or 90 ton capacities. It’s imperative that the tank cars not be loaded in excess of the load limit stenciled on the side of the car; therefore we would always recommend a secondary overfill device. The rails cars themselves have a 10′ outside diameter and an overall length ranging from 33’ to 48’, with a 6’x6′ centered crash box.
DOT MC-330 & MC-331 tank trailers are used to transport chlorine over roads and highways with a capacity of 15 – 20 tons (13,600 kg – 20,000 kg) The trailers can be top or bottom loaded/unloaded using the same man way and valve arrangements as rail tank cars and are required to have excess flow check valves under both the liquid and gas angle valves. Before loading begins, all hoses and ANSI fittings should be connected to the trailer for accurate axle weight to prevent overfilling.
Your Project
Typically, as a starting point, we will need to know answers to these questions for your project
- The Railcar connection locations need flexibility – Do you know what the breadbasket connections look like?
- Are you using liquid and vapor arms/hose as two separate devices or a piggyback arm?
- Is the loading station indoors or outdoors?
- Is the loading area temperature controlled?
- How are you going to spot your railcars
Our highly trained technical sales team will undertake a detailed site survey prior to undertaking any work to check and clarify all dimensions, obstructions, access issues and other salient points. Our challenge is to provide the safest working environment – protecting operators and the equipment – while simultaneously enabling you to improve throughput and productivity.
Your Project Needs
Whether you are looking for a turn-key installation, on-site supervision or a maintenance program, SafeRack is positioned to assist you. We can do as little or as much as you need. Our project management and supervision team is the best in the business at supporting your company’s needs.
- Collaborative Design – Our loading platform specialists will work with you one on one, if you design to design the best loading solution for your specific needs
- Contract review – drawings and associated documents relating to the contract prior to site arrival
- Risk Assessment – Undertaking a site risk assessment
- Shipment Inspection – Detection of any shipping damage or abnormalities
- Material Receiving – Supervised off-loading and transport at site
- Installation Management – Supervised Installations and Coordination
- Start-up & Commissioning – On-site training for both users and maintenance personnel
Loading Arms
Generally speaking, SafeRack recommends rigid pipe loading arms where possible for the following reasons:
- Balanced throughout their movement envelope
- Designed not to hit the ground – protecting the asset and the operator
- Ergonomic – one man operation
- Fitted with manual or actuated valves.
- Fitted with optional purge/vent facilities
- Can be moved into position with ease and left hanging in the air while the operator prepares the tanker connection
- Parked neatly
Hoses require:
- Annual pressure test
- Are difficult to stow neatly when not in use
- Can be dropped
- Can be driven over
- Are very heavy to use if fitted with a valve at the tanker connection point
- Cannot be easily heated or have vent/purge valves fitted to it
- Prone to catastrophic failure
Typical Chlorine Loading Platform
Quote or discuss your installation.
Start by selecting loading application"*" indicates required fields
Below are some of the loading and unloading solutions for illustrative purposes only. Our experts will work with you and your team for a custom solution to suit your needs.
Chlorine Loading
Chlorine is typically loaded into railcars and road trailers via chemical hoses. The current best loading practice is to use a PTFE lined chemical hose, with a quick-acting coupling, often in the form of Hammer Unions with a stabber pipe.
In the U.S. loading arms are generally not used for the transfer of liquid chlorine, due to cost and long-term maintenance issues. By-pass arms however, can be used to support the chlorine hose, making it easier to handle. Likewise, you also have the option to use a hose carrier. Emergency Shut-off Valves (ESV’s) can also be fitted near the inlet of the hose for additional safety in the event of a leak, rupture or drive-off.
Loading Gangways and Safety Cages
A wider access gangway (36″-48″ is preferable) as it helps improve access and egress to and from the vessel. In addition, a wider gangway will reduce the risk of the operator’s PPE getting caught, torn or damaged, and will improve productivity and safety. Powered gangway solutions are also an option, with both hydraulic and pneumatic solutions being commonly used. Each gangway will be fitted with a two-rail safety cage for the railcar crash box. This will be a centered 6’x6’ safety cage to sit directly over the cashbox. This will provide a safe, secure work environment for your operator when connected to their breathing apparatus
SafeRack’s GX SAS gangways use Retractalok power-assist technology allowing operators to raise or lower effortlessly, light as a feather to lift, and solid as a rock. Tested in the most critical applications, this revolutionary new gangway outperforms all others. Available in multiple lengths and widths.
Learn MoreMAXRack Elevating Safety Cage
As an alternative to our two and four-rail safety cages, some customers prefer our MAXRack elevating safety cages. The ultimate fall prevention solution engineered to keep operators safe and productive. Designed for both trucks or railcars, and available in multiple cage lengths and widths. Safe, durable, and easy to use. MAXRack is built rock-solid with galvanized steel column supports and lifting arms (cages can be Aluminum, Galvanized, or Stainless Steel depending on application) Available in two power options – Pneumatic Air Drive and Electric Drive (Explosion and Non-Explosion Proof).
Learn MoreChlorine Eye Wash/Drench Showers
ANSI guidelines state that an Eye Wash/Drench Showers need to be located 10 seconds or 55’ (16.8m) from contaminants or hazardous materials. Eyewash stations need to be on the same horizontal plane with no obstructions.
Therefore, we would propose the installation of a standard combination Drench Shower/Eyewash Unit, which will save limited space and fit easily into any work environment.
Chlorine Spill Containment
Spill containment pans will be provided at the point of loading operations and is an essential piece of equipment in overall site safety and environmental protection. Chlorine Grounding
While chlorine is not flammable, industry best practice includes the grounding of all vessels before starting the (un)loading process. - Vehicle grounding and bonding — ensure true grounding before product flow is permitted
- Explosion-proof enclosures — meet or exceed UL, CSA and Ex requirements
Chlorine Safety Gates
Safety Gates will be installed at the top of stairs and any other openings to ensure operator safety at all times. YellowGate Safety Gates
SafeRack’s line of industrial safety gates is the most flexible product on the market with the ability span openings between 16” and 36” and is field adjustable with nothing more than a wrench. Learn More
Chlorine Options
- Lighting – Lighting both over and under the platform will be provided. For overcast days or second shift, lighting is essential for improved safety and improved productivity.
- Platform & Canopies – Full platform canopies reduce exposure to the elements and improve the safe and productive loading operation from the operator’s perspective.
- Operator Shelter – Depending on your site requirements, consideration should be given to the requirement of an operator or guard building on the loading platform. This can be customized to meet specific site requirements
- Wheel Chocks – Railcar Wheel Chocks provide fast blocking of all types of railcars and meet OSHA regulations to safely prevent railroad cars from moving during loading or unloading operations. This is a requirement by the Department of Homeland Security
Personal Protective Equipment PPE Requirements
Eye/Face Protection: Wear chemical safety goggles. A face shield (with safety goggles) may also be necessary.
Skin Protection: Wear chemical protective clothing e.g. gloves, aprons, boots. Coveralls or long sleeve shirts and pants in some operations. Wear a chemical protective, full-body encapsulating suit, and self-contained breathing apparatus (SCBA). Suitable materials include: butyl rubber, neoprene rubber, Viton®, Viton®/butyl rubber, Barrier® – PE/PA/PE, Silver Shield® – PE/EVAL/PE, Trellchem® HPS, Trellchem® VPS, Saranex®™, Tychem® BR/LV, Tychem® Responder® CSM, Tychem® TK. The following materials should NOT be used: natural rubber, polyvinyl chloride. Recommendations are NOT valid for very thin neoprene rubber gloves (0.3 mm or less).
Respiratory Protection: Up to 5 ppm:
(APF = 10) Any chemical cartridge respirator with cartridge(s) providing protection against chlorine*; or Any supplied-air respirator*.
*Reported to cause eye irritation or damage; may require eye protection.
APF = Assigned Protection Factor
Recommendations apply only to National Institute for Occupational Safety and Health (NIOSH) approved respirators. Refer to the NIOSH pocket guide to chemical hazards for more information.
Use a local exhaust ventilation and enclosure, if necessary, to control the amount in the air. Consider using a corrosion-resistant exhaust ventilation system separate from other ventilation systems. It may be necessary to use stringent control measures such as process enclosure to prevent product release into the workplace. Use backup controls (e.g. double mechanical pump seals) to prevent the release of this material due to equipment failure. * For illustrative purposes only. Our experts will work with you and your team for a custom solution to suit your needs We recommend that you also refer to the Chlorine Institute, found at chlorineinstitute.org. The Chlorine Institute (CI) was founded in 1924 and is a technical trade association of companies involved in the safe production, distribution, and use of chlorine, sodium and potassium hydroxides and sodium hypochlorite, the distribution and use of hydrogen chloride and the distribution of vinyl chloride monomer.
Customer Reviews
5 5Recommended for cost and ease of installation.Product was delivered within a week. Good quality that serves my need. I would recommend this product for cost and ease of installation.
By Buddy McCumbers from Georgia-Pacific Passport on 9/19/135 5The order was delivered within just a few days.The order was delivered within just a few days. My sales rep was very responsive and I always received prompt service. The biggest benefits are safety when climbing, ease of use and product quality. All was excellent.
By Ralph Hixon from W Smith Cartage Company Inc on 7/8/165 5Jeff Girard did an excellent job with the presentation of different models.Jeff Girard did an excellent job with the presentation of different models, giving us a good idea what we needed to purchase for our needs. The product meets the plant needs, easy stair access, easy to move from one spot to another, fall protection rails fit most all trucks.
By Howard Wilkinson from REG Geismer on 9/9/145 5Good price, and no issues.Satisfaction… they fit right back into place like the old one… good price, and no issues.
By Ivan Tramel from NuStar Logistics, L.P. on 1/7/165 5Only took a few days. Great service!We value people at our company, and we want everyone going home safe. The cost of the product is a whole lot cheaper than days away from work, pain and suffering and missed enjoyment of your employees home life. I’m really pleased.
By Michael Duff from Kinder Morgan on 2/15/185 5SafeRack came through!We had to do some gap filling on the ramp for our railcar fall protection unit. Your competitors could not supply the necessary products in time, but SafeRack came through with the add-ons……in time! Delivery time was as expected. Stephen Todd is always on top of things, keeping me informed. His communication throughout the project was excellent. We would recommend SafeRack because they supply good products.
By Dan Powell from Hexion, Inc. on 1/4/17Chlorine 101
Things to know about Chlorine
Chlorine is regulated by the U.S. Department of Transportation (DOT) and is classified as a hazardous material, with the DOT identification number UN 1017.
Chlorine is transported as a liquefied gas, under its own vapor pressure, via trucks and tank cars. Since the 1950’s the largest use for chlorine was in the manufacture of ethylene oxide and glycol (antifreeze fluids) It’s also used to make hundreds of consumer products ranging from paper products to paints, and from textiles to insecticides.
When liquid chlorine is released, it quickly turns into a gas (yellow-green in color) that stays close to the ground and spreads rapidly. Chlorine itself is not flammable, but it can react explosively when exposed to ammonia or turpentine. Exposure to chlorine can kill you by dissolving the lining of your lungs, so you can’t breathe. On the other hand, chlorine added to a swimming pool is diluted to the point where it’s only very mildly toxic.
OSHA Permissible Exposure Limit (PEL) @ .05 parts per million
Is your plant or facility compliant with ANSI, OSHA, and local safety codes? We can help!
EMERGENCY EYEWASHES / SHOWER EQUIPMENT AND THE ANSI/ISEA Z358.1 – 2014 STANDARD
Following eye contact, you must start washing with water immediately to prevent permanent damage. In the event of skin contact, you must start washing with water immediately to prevent slow-healing chemical burns.
Are you aware that ANSI guidelines state that Eye Wash/Drench Showers need to be located 10 seconds or 55′ from contaminates or hazardous materials and located on the same horizontal plane, with no obstructions? If bottom loading/unloading, an additional shower should be located at grade as well. SafeRack provides the above equipment plus much more needed to keep employees safe and expedite bulk chemical loading and unloading.
OSHA Regulation Experts – Does your existing chemical safety equipment or chemical loading systems meet OSHA’s latest requirements? SafeRack’s professional technical sales consultants are available to meet with your team to make recommendations to keep your facility in front of OSHA’s ever-changing country and region-specific standards and regulations, including lifeline and trolley beam fall arrest systems, metal stairs, and access platforms.
Why SafeRack?
The SafeRack approach is a collaborative one. Let’s call it The SafeRack Way. We have, over many years amassed a great deal of experience and understanding of the safety aspects involved in loading road tankers and railcars, as well as the behavioral habits of the operators.
Experts In Chemical Loading
- Acetic Acid
- Acetic Anhydride
- Acetonitrile
- Acrolein
- Acrylic Acid
- Acrylonitrile
- Aluminum Chloride
- Aluminum Sulfate
- Ammonia
- Ammonium Hydroxide
- Ammonium Nitrate
- Aniline
- Benzene
- Benzyl Chloride
- Bromotrifluoromethane
- Butadiene
- Carbon Dioxide
- Caustic
- Chlorine
- Chloroform
- Chlorosulfonic Acid
- DEF (Diesel Exhaust Fluid)
- Diethylene Glycol
- Dimethylformamide
- Dodecylbenzene Sulfonic Acid
- Ethanol
- Ethyl Acetate
- Ethyl Chloride
- Ethylene
- Ethylene Dichloride
- Ethylene Glycol
- Ethylene Oxide
- Ferric Chloride
- Ferrous Chloride
- Hexane
- Hydrochloric Acid
- Hydrofluoric Acid
- Hydrofluorosilicic Acid
- Hydrogen Cyanide
- Hydrogen Peroxide
- Hydrofluoric Acid
- Hypochlorous Acid
- Isopropyl Acetate
- Liquid Argon
- Liquid Nitrogen
- Liquid Oxygen
- Maleic Anhydride
- MDI
- Methanol
- Methyl Chloride
- Methyl Ethyl Ketone
- Methyl Methacrylate
- Methyl Isocyanate
- Molten Sulphur
- Nitric Acid
- Oleum
- Phenol
- Phosphoric Acid
- Phosphorus Oxychloride
- Phosphorus Trichloride
- Polypropylene
- Renewable Diesel
- Sodium Cyanide
- Sodium Hydroxide
- Sodium Hypochlorite
- Styrene Monomer
- Sulfuric Acid
- Sulfur Dioxide
- Titanium Tetrachloride
- Toluene
- Toluene Diisocyanate
- Turpenitne
- UAN (Urea Ammonium Nitrate)
- UREA
- Vinyl Acetate
- Vinyl Chloride
- Xylene
- Zinc Chloride
- Agro-Chemical
- Specialty Chemical
- Petrochemical
North America’s largest loading terminal
World-leading designer, manufacturer, and installer of truck and railcar loading platforms
As one of the primary railcar loading points, Hardisty is one of the major crude oil hubs in North America and a major origination point of pipelines that export to the United States. SCS was asked to supply and construct a SafeRack crude oil loadout terminal spanning nearly half a mile. The USD Hardisty terminal can load up to two 120-railcar unit trains per day and consists of a fixed loading rack with 62 railcar loading positions enclosed, separate control, operator, and mechanical buildings, as well as a unit train staging area and loop tracks capable of holding multiple unit trains simultaneously. SCS also supplied and installed boom-supported loading arms with supply and vapor management systems.


Quick Quote 866-761-7225
LET US DESIGN YOUR SOLUTION TODAY
Our innovative tools provide 3D visualizations and accurate quotes in minutes.
Get Help NowOrder Now 866-761-7225
Questions or Need a Quote?
Chat live with a knowledgeable and friendly safety expert now.

Bob Kashtan
Located in South Carolina

Joey Robinson
Located in South Carolina

Caelin Lacy
Located in South Carolina

Katie Kelly
Located in South Carolina

Amber Graham
Located in South Carolina